This page is about the BMW motorcycle models R26, R27, R50, R60, R69, R50/2,
R60/2, R50S, R69S, R50/US, R60/US, R69US, R50/5, R60/5, R75/5, R50/6, R60/6,
R75/6, R90/6, R90S, R60/7, R75/7, R80/7, R100/7, R100S, R100RS. These
tests apply to all models to some extent. You may have to improvise a bit.
The /5, /6 and /7 rear shocks come apart the same way.
The quick shock test
You may make a quick test that will show gross failure of the shocks.
Bounce the bike while sitting on it. Does it bounce in the rear or is it
really well damped down? With the bike on the center stand, grab a shock in the
middle, just under the shock cover and move it sideways. Is it loose or
tight? Can you see evidence of oil running down the sides of the shock? Do these
tests frequently and you will learn how it should feel. Then, when you
find that when it is different,
you may want to do some of the maintenance shown below.
Read both the one and two person disassembly and decide which is best for
you. The spring is under some compression. It is necessary to
compress it a bit more to take it apart. With understanding and care it is
easy and safe. If you do this all of the time, maybe a real tool is worth
it. With 4 full time mechanics doing only BMW work, we didn't buy the
tool at first. Here is what we did.
One person disassembly of the BMW motorcycle front shock for Earles forks.
If only one person is available to disassemble the shock, here is how to do
it. This can be done without damaging the paint.
Put the shock bottom in a vise with cloth to protect the metal. Push
the bottom of the upper shock cover to one side to make a small gap at the top.
Use a small flat blade screwdriver to get in the gap. I usually use a
screwdriver that I have rounded off the sharp edges to keep from scratching the
parts. Sometimes I wrapped it in tape. Sorry, but the only shocks I
currently have to photograph are these old ugly ones. Don't despair, they
can be cleaned up to look very good.
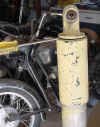
Now, lever the cover down to get two larger flat blade
screwdrivers in, one on each side. Protect the paint.
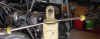
Turn them so that they are edgewise and hold the can as far down as possible.
The paint is not worth protecting on this shock. You may need to change
screwdrivers or use pieces or wood to hold the can down. The idea is to
put larger and larger pieces in to hold the cover down more and more.
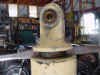
This should give you access to the 2 or 3 round rubber donuts, just under the
top piece and on the round shaft. Move the rubber bumpers down to get
access to the round shaft. That will expose the two flat places milled on
the shaft for a 9 mm open end wrench. Use a 9 mm open end wrench on the
flats and a round Tommy bar in the hole of the top piece. Wrap tape around the
wrench to protect the paint. The wrench will hold the spring compressed
and the tools can be removed.
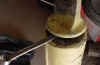
You may be able to now turn the top piece off, but probably not. Use a
propane torch to heat it up. No matter how you compress the spring, you
may need heat to get the top casting off.
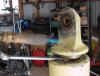
Avoid burning the rubber in the top bushing. Get the temperature up to
water boiling (read; sizzle spit) and that should be enough to turn the top off.
Let it cool gradually. With one hand holding the cover down, carefully
remove the 9 mm wrench with the other. Remove the cover and spring.
Two person disassembly
Put the shock upright in a vise and tighten it on the bottom (eye) mounting
part. Grab the can, or shock cover, with both hands and pull down against
the spring. It must be pulled down about 1," Have your helper use a
screwdriver to slide the rubber donuts down 1/2," to expose the shaft. Now
slip a 9 mm open end wrench onto the two flats that are on the shaft. With
the wrench on the flats, the can no longer needs to be held. The wrench
will hold the can down and therefore the compressed spring. Put a round (tommy)
bar in the top (eye) mounting hole and unscrew the top. The aluminum top
will usually need some heat to free it up.
Testing the Boge hydraulic unit
With the top off, compress the can, remove the wrench and the carefully
release pressure on the spring. Remove the spring. Screw the top
back onto the shaft a bit, as this gives you a place to grab. Slowly move
the shaft up and down several times. If you feel any "free" places, then
it is bad. The pressure required to go one way isn't the same as the other
way. It should go in easily and come out much harder. For this test
it must be vertical, which is the normal operating position.
To remove the hydraulic unit, (/2) I use a strap wrench. It won't crush
the unit. If it is to be replaced anyway then a pipe wrench may be used.
Heat may be needed, but only on the aluminum casting, not the steel hydraulic
unit.
Your first one may be a struggle, but all of the rest of them will be easy.
The /6's are much harder to remove, due to a change in the top piece. The
spring must be compressed much more. It takes two persons for sure.
I highly recommend inspecting the holes in the covers where they barely slip
over the castings. You really need to remove any burrs. Make sure
that they slip on and off easily. This will make it easier to assemble.
To reassemble, one must use heat on the /2 aluminum parts or they will later
unscrew. The /5 needs some serious torque or use Locktite (glue) as it can
unscrew too.
Upon reassembly, inspect the place where the top and bottom covers telescope
together. If they aren't aligned properly, They will rub together and self
destruct. See photo.
See the large gap on the left side and almost nothing on the right side? If
they are not equalized, you run a good chance of them rubbing against each
other. I have seen them wear completely through the metal. The same
thing applies to the rear of the /2.
Occasionally I have been able to rotate the cover and fix the gap error.
Usually this doesn't work and it must be shimmed.
This paragraph applies to the photo above. With your thumb on the lower
left side, push over towards the right side. In the crack created, up at
the top, where you first inserted the small screwdriver, Now insert a shim.
I have used a variety of materials, but found that old playing cards work well.
They don't compress or decompose with time. Cut as needed to make them
invisible. Use the thickness that gives you equal space all of the way
around.
The rubber mounting bushings can be easily changed if needed. They are
usually good for a long time. The ones shown are in poor condition, but
will work. If no press is available, use sockets and a vise. One
socket slightly smaller than the bushing to do the pushing and another socket
with an inside that is larger than the OD of the bushing. I guess one
could hammer them in and out, but that is crude.
I have seen 2 and 3 rubber bumpers. They are the rubber donut pieces on
the shaft of the hydraulic unit. They serve as a limit to the compression
end of travel of the front end. Some bikes have 2 on one shock and 3 on
the other. It could be some kind of progressive stopping thing. I
have never had to replace them because they wore out.
Removing the /2 BMW motorcycle rear shocks
The rear shocks have an polished aluminum cover at the top. The cap is
cosmetic and also keeps rain from rusting the rod and nut at the shock top.
Sometimes the cap can be hard to remove. The stock toolkit has a spanner
wrench (American lingo) that fits into any of the 4 holes and turns the cap.
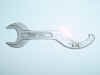
An original spanner from the tool kit.
This is just a leftover tool and not what I used. This tool also
removes the exhaust nut. It has the wrong radius for the rear shock cap.
See the two pins in the middle of the curve? They are for adjusting the rear
swing arm preload. I would grind that part of the curve deeper to reduce
the radius. Then it fits the cap.
The cap often gets stuck to the hydraulic unit rod. It will just turn
and turn. At the first sign of spinning, stop. You will only make it
worse. The most common solution is to apply heat to the top of the cap.
Heat it in the top center with a propane gas type torch. Use the spanner
and hit it sharply with a steel hammer. That should pop it loose.
You may have to try more heat, probably well above the boiling temperature of
boiling water. Don't use a rubber or plastic mallet. You want as
much of a "shock" as possible.
If heat fails, you may have to damage or destroy the cap. Drill a small
hole down into the center. That allows you access to the top of the
threads. If the frame is bare, then it is easy to also turn it upside down
and soak from the bottom too. Soak it well with your favorite penetrant
for a few days. Now try the heat again. If that fails, then drill a
hole that is large enough to get a slot screwdriver into. The top of the
rod has a screwdriver slot in it. This allows one to hold the rod while
tightening the locking nut upon assembly. Use that slot to hold the rod
from turning. Always use heat as needed.
In the worst case, you may need to cut the cap off. That is rarely
needed. Once off, you can now polish it easily. It will go back on
easily and work well. The caps are available new from Mobile Traditions.
The hole in the cap can be welded up to save it.
Feedback from Eric, I haven't tried it, but it sounds great.
I thought I might share a recent episode with the group in case it might help
a few here or there. I bought some shock covers to put on my coverless
shocks and started the project last night. I have read Duane's article on
one person and two person disassembly and thought I'd have a go on the one
person version. Not being a big fan of torches (call me a wussie) I went
to one of the guys out in the shop (I sell garbage trucks and we have a six bay
garage here to service them) to see how we could take a little bitty 9mm wrench
and get the top off the shock off. He said, "heat it." After explaining my
wussieness, he then handed me a 2 1/2 foot skinny steel pipe. "Leverage,"
he said. In the absence of a spring compressor, he also handed me a couple
of nylon ties to feed through the spring and tighten them up a bit. Worked
like a charm. I stuck the head of the shock in the vise and went to work.
The ties pulled the springs down about an inch and a half and I stuck the pipe
over the 9mm wrench and.....viola!!!...... the rod was loose in no time.
This was by far the quickest job I've done on a motorcycle.
I'm sure this was thought of before, just thought I'd share my miniscule
triumph.
-Eric
|