I removed the mechanical advance unit from my ‘69 R60US BMW motorcycle,
with about 30K miles on it, and built a device to measure the timing curve that
it follows. Below is a graph of my results. The upper line if the
curve we got as RPM decreased while the lower line is the curve that was
generated as the RPM was increased. The difference between the two lines
is probably the result of “stiction” in the advance mechanism. The graphed
data is the result of two runs, up and back down, with the RPM being measure
every 2.5° at the camshaft or 5° at the crankshaft. (NOTE: Since the
advance unit is attached to the camshaft both the measured rotational rate and
degrees of advance must be doubled when we talk about these values relative to
the crankshaft.)
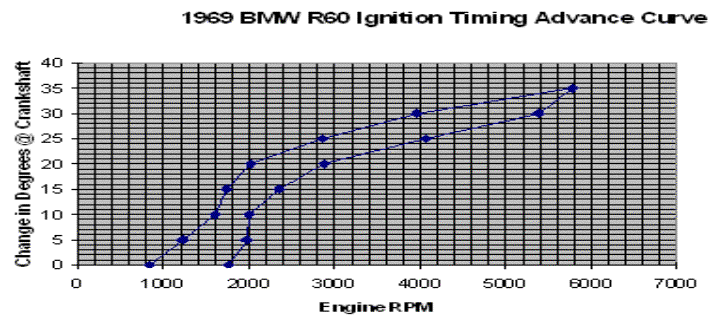
The manual, which came with the motorcycle, has the following to say about
timing: Ignition timing - 9° BTDC (governor weights in neutral position).
Range of adjustment - 30° at crankshaft. Max advance - 39° ±2° BTDC.
Since static timing is set for 9°, we need to add the change in degrees, shown
in the chart above, to 9° in order to find how many degrees BTDC the ignition
system is fired by this particular advance unit. If we want to find the
maximum advance provided by this unit we need to add 35° to 9° and come up with
44° of maximum advance! This is out of spec. by 3° since the maximum
allowed advance is 39° ±2° = 41°. As a result, the data my son and I
collected should not be considered sacred.
As I think about the results of our testing, I am struck by how crude the
advance mechanism is. The stiction results in sloppy timing as can be seen
from the graph. Secondly, things like stiction are amplified by a factor
of two because the mechanism is mounted to the camshaft, not the crankshaft.
If my advance mechanism is any indication of the advance units built for the
R60’s, then I feel it’s a pretty imprecise system. On the other hand, my
advance unit could be bad or it may simply not matter. Either way, my test
fixture showed me how the advance unit works and it makes spotting a flaky
advance unit pretty simple. The hysteresis between increasing and
decreasing RPM was obvious from the git-go, even without a tachometer.
Device for measuring advance:
The device I built to make these measurements as kept as simple as possible
without sacrificing accuracy. I used what I had and it wound up not
costing me a cent. Your mileage may vary.
The basic concept was to spin the advance unit up to 4,000 RPM while it was
mounted to a wheel marked off in degrees. The wheel I happened to have was
marked off for a full 360°. I decided that a frequency counter would be a
good, quick, way to measure RPM. I had one that would measure from 1 to
500 MHz. I thought it would be easier to have the counter read out in RPM
so, using CAD, I drew up an encoder wheel with 60 black and white bars around
the circumference. This encoder wheel was then attached to the bottom of
the degree wheel. I happened to have several non-contact bar code readers
so I used one to read the black and white lines on the bottom of my degree
wheel. The output was run to the frequency counter and I was reading RPM!
I turned a little arbor to hold the advance unit and the degree wheel. The
whole thing was then mounted to an old electric sewing machine motor that I had
attached to a simple plywood stand. I drew a long line on the bottom of
the degree wheel and added a second bar code reader. The output from this
reader was connected to a crude but effective triggerable strobe light I had
built, years ago, from stuff in my junk box. Once I got it working, the
strobe would flash always at the same place as the degree wheel spun. It’s
a lot easier to synchronize the strobe to the wheel than trying to read the
wheel with an asynchronous strobe! (Yes, I tried it!)
I then cut out a simple double-ended pointer, to keep things balanced, and
glued it to the advance unit, just below the cam, to work as my indicator.
Below are two shots of my setup:
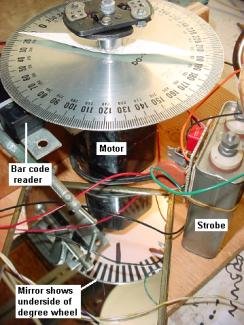
1969
BMW Magneto Ignition Advance Unit Analysis
By
Klaus
Wolter, 11/23/01
I removed the mechanical advance unit from
my ‘69 R60US BMW motorcycle, with about 30K miles on it, and built a device to
measure the timing curve that it follows.
Below is a graph of my results.
The upper line if the curve we got as RPM decreased while the lower line is the
curve that was generated as the RPM was increased.
The difference between the two lines is probably the result of “stiction” in the
advance mechanism. The graphed data
is the result of two runs, up and back down, with the RPM being measure every
2.5° at the camshaft or 5° at the crankshaft. (NOTE: Since the advance unit is attached to the camshaft both the
measured rotational rate and degrees of advance must be doubled when we talk
about these values relative to the crankshaft.)
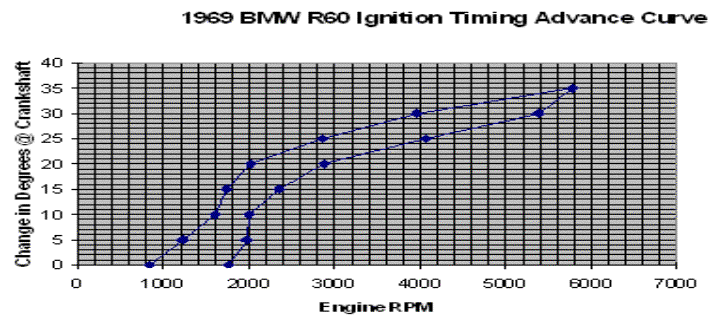
The manual, which came with the motorcycle,
has the following to say about timing: Ignition
timing - 9° BTDC (governor weights in neutral position).
Range of adjustment - 30° at crankshaft.
Max advance - 39° ±2° BTDC. Since
static timing is set for 9°, we need to add the change in degrees, shown in the
chart above, to 9° in order to find how many degrees BTDC the ignition system is
fired by this particular advance unit. If
we want to find the maximum advance provided by this unit we need to add 35° to
9° and come up with 44° of maximum advance!
This is out of spec. by 3° since the maximum allowed advance is 39°
±2° = 41°. As a result, the data my
son and I collected should not be considered sacred.
As I think about the results of our testing,
I am struck by how crude the advance mechanism is.
The stiction results in sloppy timing as can be seen from the graph.
Secondly, things like stiction are amplified by a factor of two because
the mechanism is mounted to the camshaft, not the crankshaft.
If my advance mechanism is any indication of the advance units built for
the R60’s, then I feel it’s a pretty imprecise system.
On the other hand, my advance unit could be bad or it may simply not
matter. Either way, my test
fixture showed me how the advance unit works and it makes spotting a flaky
advance unit pretty simple. The hysteresis between
increasing and decreasing RPM was obvious from the git-go, even without a
tachometer.
Device
for measuring advance:
The device I built to make these
measurements as kept as simple as possible without sacrificing accuracy.
I used what I had and it wound up not costing me a cent.
Your mileage may vary.
The basic concept was to spin the advance
unit up to 4,000 RPM while it was mounted to a wheel marked off in degrees.
The wheel I happened to have was marked off for a full 360°.
I decided that a frequency counter would be a good, quick, way to measure
RPM. I had one that would
measure from 1 to 500 MHz. I
thought it would be easier to have the counter read out in RPM so, using CAD, I
drew up an encoder wheel with 60 black and white bars around the circumference.
This encoder wheel was then attached to the bottom of the degree wheel.
I happened to have several non-contact bar code readers so I used one to
read the black and white lines on the bottom of my degree wheel.
The output was run to the frequency counter and I was reading RPM!
I turned a little arbor to hold the advance unit and the degree wheel.
The whole thing was then mounted to an old electric sewing machine motor
that I had attached to a simple plywood stand.
I drew a long line on the bottom of the degree wheel and added a second
bar code reader. The output from
this reader was connected to a crude but effective triggerable strobe light I
had built, years ago, from stuff in my junk box.
Once I got it working, the strobe would flash always at the same place as
the degree wheel spun. It’s a lot
easier to synchronize the strobe to the wheel than trying to read the wheel with
an asynchronous strobe! (Yes, I
tried it!)
I then cut out a simple double-ended
pointer, to keep things balanced, and glued it to the advance unit, just below
the cam, to work as my indicator.
Below are two shots of my setup:
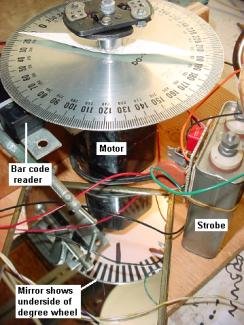
Data:
My 12 year old son, Keane, recorded the data as I manipulated a variac that
controlled the speed of the electric motor. Below is the data that we
entered in to a spreadsheet and manipulated. This data generated the graph
shown above.
Degrees
|
RPM
#1
|
RPM
#2
|
Difference
|
Average
RPM
|
Engine
RPM
|
Degrees
@ engine
|
0
|
900
|
860
|
40
|
880
|
1760
|
0
|
2.5
|
950
|
1020
|
-70
|
985
|
1970
|
5
|
5
|
1000
|
1000
|
0
|
1000
|
2000
|
10
|
7.5
|
1150
|
1200
|
-50
|
1175
|
2350
|
15
|
10
|
1450
|
1430
|
20
|
1440
|
2880
|
20
|
12.5
|
2000
|
2060
|
-60
|
2030
|
4060
|
25
|
15
|
2700
|
2680
|
20
|
2690
|
5380
|
30
|
17.5
|
2900
|
2880
|
20
|
2890
|
5780
|
35
|
15
|
2000
|
1960
|
40
|
1980
|
3960
|
30
|
12.5
|
1450
|
1410
|
40
|
1430
|
2860
|
25
|
10
|
1010
|
1010
|
0
|
1010
|
2020
|
20
|
7.5
|
850
|
880
|
-30
|
865
|
1730
|
15
|
5
|
800
|
800
|
0
|
800
|
1600
|
10
|
2.5
|
620
|
600
|
20
|
610
|
1220
|
5
|
0
|
440
|
400
|
40
|
420
|
840
|
0
|
Key:
Degrees - How many degrees the pointer moved from 0 on the test fixture.
RPM #1 - RPM of the test fixture. This was our first pass.
RPM #2 - RPM of the test fixture. This was our second pass.
Difference - Difference in RPM from first to second pass. (RPM #1 - RPM
#2)
Average - Average RPM from the two passes.
Engine RPM - The average RPM X 2 for crankshaft RPM.
Degrees @ engine - Degrees at cam X 2 for degrees relative to the crankshaft.
My thanks to Klaus for taking his time and expertise to assist the greater /2
community. He has also done far more than just this one project.
They are a family that I respect greatly.
|