A philosophy of torque on a BMW motorcycle
The main reason for a spec on tightness is to prevent over tightening, not
under tightening. In the case of multiple fasteners on one part, it is
also to prevent warping.
Carefully check for the torque on the part that you are tightening or
loosening. One of the BMW shop manuals had incorrect torque settings in it. Some
of the after market books have not always gotten it correct. Use common sense
and double check it. At a glance, I see some good information on
snowbum's page about
torque values.
Aluminum is especially sensitive, as it has some odd characteristics. I am
not any kind of expert in the area of metallurgy, but I have learned a few
things. For example, BMW hand levers can be straightened with gentle slow
pressure in a warm room. This is due to a characteristic called "cold flow." The
Japanese levers usually break when straightened. The cases where they do
straighten one is followed with stories of hearing a "clink" and then finding
the piece on the floor. The BMW lever (Magura) is (was) the best around. I have
straightened them when they were bent
double. Has it changed in the last 25 years?
A major aluminum problem for BMW was the heads on
the /2 in the starting in the early/mid 60s.
The valve cover center stud is subject to over tightening too. It should only
be tight enough that it doesn't fall off. Just beyond finger tight. Over
tightening pulls the stud put of the head and that means some rethreading
procedure must be used. It is far better to lose the nut and washer than stripe
out the head. Then you will lose the nut, washer and stud. Then it is time to
use a Heli-coil or other thread repair procedure.
Axle nuts should be the necessary amount, which is seldom the book amount. Read my page on wheel bearings.
When I consider the amount of money that I charged, caused by incorrect
tightness, I find it shocking. We fixed problems caused by over and under
tightness. Expenses for over tightness were at least 10 times the amount of
under tightness expenses. Safety, due to over tightening, was also jeopardized
by a factor of maybe 5. I didn't keep exact records, but it wasn't even close. Over tight is bad, very bad. See my page on parts that
fall off of a BMW.
If you must err, do it on the "under tight" side. Head torque should be 25 ft
lbs. I would rather my BMW be 15 ft lbs, than 30 ft lbs.
Repairs caused by incompetence, ignorance and inattention were many times
greater than those caused by poor design, lack of inspection, cheapness and just
plain bad luck. Here are a few things not to do.
Learn how to use a torque wrench. The threads must be "clean" and able to be
run all of the way down by finger. I have seen a head bolt that was so jammed
into the head that it took 15 lbs just to turn it against the sides of the hole,
when it should have fallen out, but I had to hammer it out. It would be
impossible to torque that head bolt to anything meaningful. Learn to use slow
tightening as opposed to fast. I prefer to use my beam torque wrench, but have
to check it from time to time as they aren't famous for accuracy. The beam
type is much better for removing a fastener as it will show where it breaks
loose, a sometimes useful number.
This torque wrench may
not be the best one for use on a BMW:-)
Removing a stripped out bolt
This is a very old trick that I learned as a teenager from my grandfather.
When you find a bolt, nut or screw that seems questionable, take a second out
and think about it.
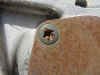
This is an example of a stripped Phillips head screw on an oil cover of a /6
engine. It looks hopeless, but it can be removed quite easily. I would use my
hand impact tool. Make absolutely sure that you have the correct sized bit. Then
dip the end into valve grinding paste. The paste is made up of ground up
silicate, or common sand. The small particles will take up a bit of space, but
mostly they will really grab both the Phillips tip and the seemingly ruined
screw. Hold the impact tool tightly and give it small taps at first to see that
the tip seats as well as it possibly can into the screw head. Hold the impact in
the direction for unscrewing or counter clockwise for most fasteners. Now
give it a hit.
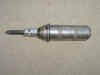
This is my impact tool that I have used for more than 40 years. It is
currently fitted with a Phillips tip. This trick with valve grinding paste
will also work on slot screws and hex head bolts.
|